Information from the National Ready Mixed Concrete Association
WHAT is Dusting?
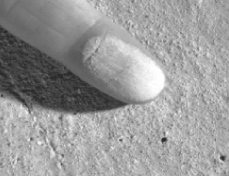
Dusting Concrete Surface
- They powder under any kind of traffic
- They can be easily scratched with a nail or even by sweeping
WHY Do Concrete Floors Dust?
A concrete floor dusts under traffic because the wearing surface is weak. This weakness is caused by:
- Any finishing operation performed while bleed water is on the surface or before the concrete has finished bleeding. Working this bleed water back into the top 1/4 inch [6 mm] of the slab produces a very high water-cement ratio and, therefore, a low strength surface layer.
- Placement over a non-absorptive subgrade or polyethylene vapor retarder. This reduces normal absorption by the subgrade, increases bleeding and, as a result, the risk of surface dusting.
- Floating and/or troweling operations following the condensation of moisture from warm humid air on cold concrete. In cold weather concrete sets slowly, in particular, cold concrete in basement floors. If the humidity is relatively high, water will condense on the freshly placed concrete, which, if troweled into the surface, will cause dusting.
- Inadequate ventilation in enclosed spaces. Carbon dioxide from open salamanders, gasoline engines or generators, power buggies or mixer engines may cause a chemical reaction known as carbonation, which greatly reduces the strength and hardness of the concrete surface.
- Insufficient curing. This omission often results in a soft surface skin, which will easily dust under foot traffic.
- Inadequate protection of freshly placed concrete from rain, snow or drying winds. Allowing the concrete surface to freeze will weaken the surface and result in dusting.
HOW to Prevent Dusting
- Concrete with the lowest water content with an adequate slump for placing and finishing will result in a strong, durable, and wear-resistant surface. In general, use concrete with a moderate slump not exceeding 5 inches [125 mm]. Concrete with a higher slump may be used provided the mixture is designed to produce the required strength without excessive bleeding and/or segregation. Water-reducing admixtures are typically used to increase slump while maintaining a low water content in the mixture. This is particularly important in cold weather when delayed set results in prolonged bleeding.
- NEVER sprinkle or trowel dry cement into the surface of plastic concrete to absorb bleed water. Remove bleed water by dragging a garden hose across the surface. Excessive bleeding of concrete can be reduced by using air-entrained concrete, by modifying mix proportions, or by accelerating the setting time.
- DO NOT perform any finishing operations with water present on the surface or while the concrete continues to bleed. Initial screeding must be promptly followed by bull floating. Delaying bull floating operations can cause bleed water to be worked into surface layer. Do not use a jitterbug, as it tends to bring excess mortar to the surface. DO NOT add water.
- Do not place concrete directly on polyethylene vapor retarders or non-absorptive subgrades as this can contribute to problems such as dusting, scaling, and cracking. Place 3 to 4 inches [75 to 100 mm] of a trimmable, compactable fill, such as a crusher-run material, over vapor retarders or nonabsorptive subgrade prior to concrete placement. When high evaporation rates exist, lightly dampen absorptive subgrades just prior to concrete placement, ensuring that water does not pond or collect on the subgrade surface.
- Provide proper curing by using liquid membrane curing compound or by covering the surface with water, wet burlap, or other curing materials as soon as possible after finishing to retain moisture in the slab. It is important to protect concrete from the environment at early ages.
- Placing concrete in cold weather requires concrete temperatures exceeding 50°F [10°C] as well as an accelerating admixture.
HOW to Repair Dusting
- Sandblast, shot blast or use a high-pressure washer to remove the weak surface layer.
- To minimize or eliminate dusting, apply a commercially available chemical floor hardener, such as sodium silicate (water glass) or metallic zinc or magnesium fluosilicate, in compliance with manufacturer’s directions on thoroughly dried concrete. If dusting persists, use a coating, such as latex formulations, epoxy sealers, or cement paint.
- In severe cases, a serviceable floor can be obtained by wet-grinding the surface to durable substrate concrete. This may be followed by properly bonded placement of a topping course. If this is not practical, installation of a floor covering, such as carpeting or vinyl tile covering, is the least expensive solution to severe dusting. This option will require some prior preparation since adhesives for floor covering materials will not bond to floors with a dusting problem and dusting can permeate through carpeting.
Follow These Rules to Prevent Dusting
- Use Moderate slump concrete not exceeding 5 inches [125 mm]
- Do not start finishing operations while concrete is bleeding
- Do not broadcast cement or sprinkle water on concrete prior to or during finishing operations
- Ensure that there is adequate venting of exhaust gases from gas-fired heaters in enclosed spaces
- Use adequate curing measures to retain moisture in concrete for the first 3 to 7 days and protect it from the environment
References
- Guide for Concrete Floor and Slab Construction, ACI 302.1R. American Concrete Institute, Farmington Hills, MI.
- Slabs on Grade, Concrete Craftsman Series CCS-1, American Concrete Institute, Farmington Hills, MI
- The Effects of Various Surface Treatments, Using Zinc and Magnesium Flusilicate Crystals on Abrasions Resistance of Concrete Surfaces, Concrete Laboratory Report No. C-819, U.S. Bureau of Reclamation
- Residential Concrete, National Association of Home Builders, Washington, DC.
- Trouble Shooting Guide for Concrete Dusting, Concrete Construction, April 1996.
USED WITH PERMISSION FROM THE NRMCA